Embarking on a transformative journey, C.Steinweg Bridge is thrilled to announce the expansion of its Cape Town facility. This strategic initiative is not merely an upgrade but a pivotal step towards future growth. The redesigned facility is poised to provide superior customer service, featuring state-of-the-art facilities and a modernized infrastructure. Steinweg’s commitment to excellence shines through as the enhanced Cape Town facility promises to meet the evolving needs of clients, offering unparalleled efficiency and capabilities. Join us on this exciting venture as we redefine standards and elevate our capabilities to new heights.
In a recent interview, Warren Beckwith shed light on the ambitious expansion project underway at Steinweg’s facility in Cape Town. The focus of the expansion includes bulk fertilizer handling and a comprehensive modernization effort of the general cargo store. Warren explains the current fertilizer operations: “Bulk fertilizer parcels involve bringing in bulk shipments directly from vessels, offloading into bulk bays, and dispatching in bulk to customers. Alternatively, we bag these products, transferring from bulk to one-ton bags, 50kg bags or 25kg bags. We have both bulk ending and bagging operations, dedicated to dry fertilizer commodities, covering about 5.000 square meters.”
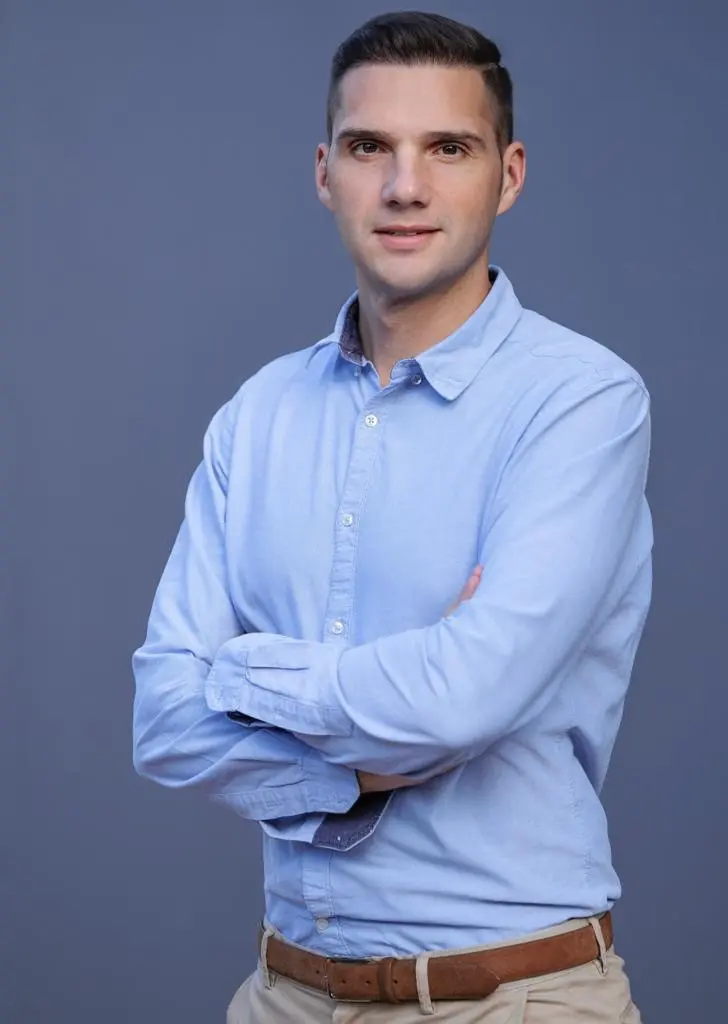
Modernizing externally and internally
Adjacent to this area is a facility of similar size, handling a range of commodities such as general cargo, reels, metal, and steel. However, Warren highlights the need for a transformation: “We’ve started a comprehensive rebuild, breaking ground in August 2023, with an expected completion date of end May 2024. The facility, although functional, currently has an outdated appearance, and our aim is to modernize it both externally and internally.”
Regarding the strategic location, Warren emphasizes: “We believe the current location has untapped potential for our customers, and hence, we decided against seeking a new location. The rebuild will feature the highest level of compliance and technology, including 24hr camera surveillance, perimeter surveillance, automated fire detection systems, overhead and in-rack water sprinkler systems, system generated product segregation, back-up power, etc. The installation of the new racks is scheduled for the first week of April 2024, providing approximately 5.000 pallet locations. Additionally, a dedicated flammable store will be established to accommodate flammable substances, expanding our service offerings.”
Significant investments and clear purpose
Warren details the technological enhancements: “The facility will feature a dedicated barcode scan operation, ensuring efficient tracking with barcode labeling for commodities. The warehouse’s physical layout will be virtually replicated within our warehouse management system. This enhances allocation accuracy, picking, and packing efficiency.”
In response to the significant investments, Warren affirms: “We are looking at a substantial investment, and the rebuild is a culmination of strategic planning. The necessity for this transformation arose from the need to specialize our Cape Town facility. We wanted to move beyond being a general goods store and give the facility a clear purpose.”
The decision-making process involved studying successful practices adopted in other facilities, the likes of Johannesburg and Durban. Warren notes: “We looked at making an extension of those facilities within the Cape Town region, ensuring a long-term purpose for the facility.” Warren acknowledges the involvement of clients in shaping the project: “Customer feedback played a crucial role. Conversations with existing and potential clients highlighted the need and direction for the redevelopment in Cape Town in order to meet local market needs.”
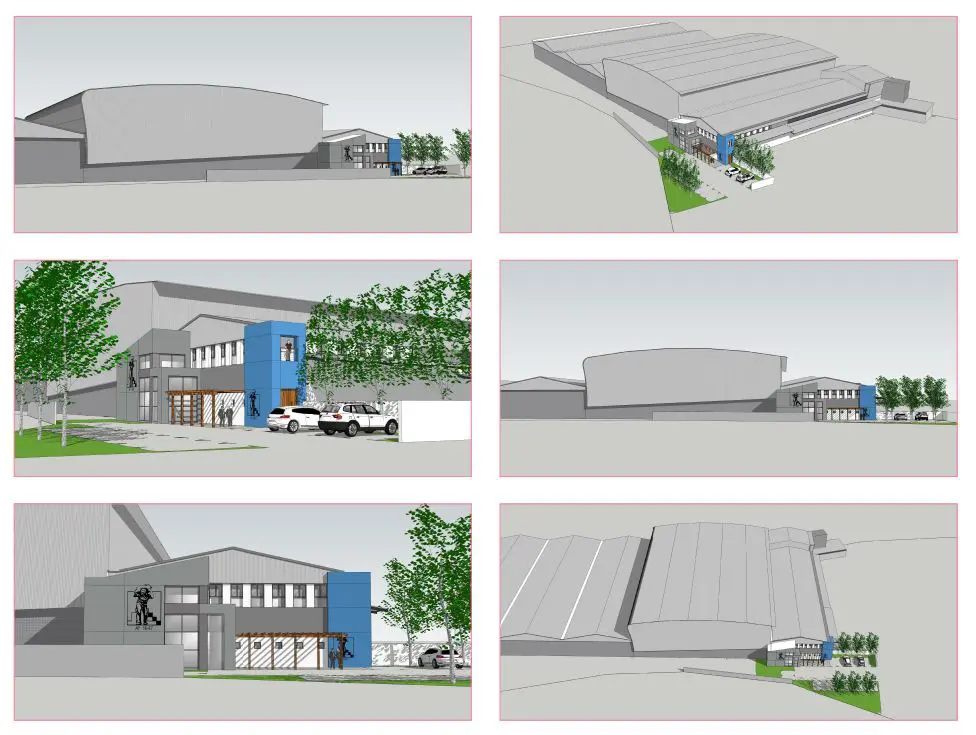
Managing ongoing challenges
The ongoing challenges in maintaining regular operations during the construction phase are acknowledged by Warren: “It’s a significant challenge, but we are managing it well and with a phased approach. The new structure is being built around the existing structure, allowing us to continue operations within the current warehouse. The phased construction involves expanding the facility gradually within the rebuild timeframe.” Warren concludes by highlighting the close collaboration with customers: “We are keeping our customers informed about the rebuild and working closely with them. Despite the challenges, we aim to excite our customers about the forthcoming benefits of the modernized facility, which should give them the edge within their supply chain.”
Published on: 12 December 2023